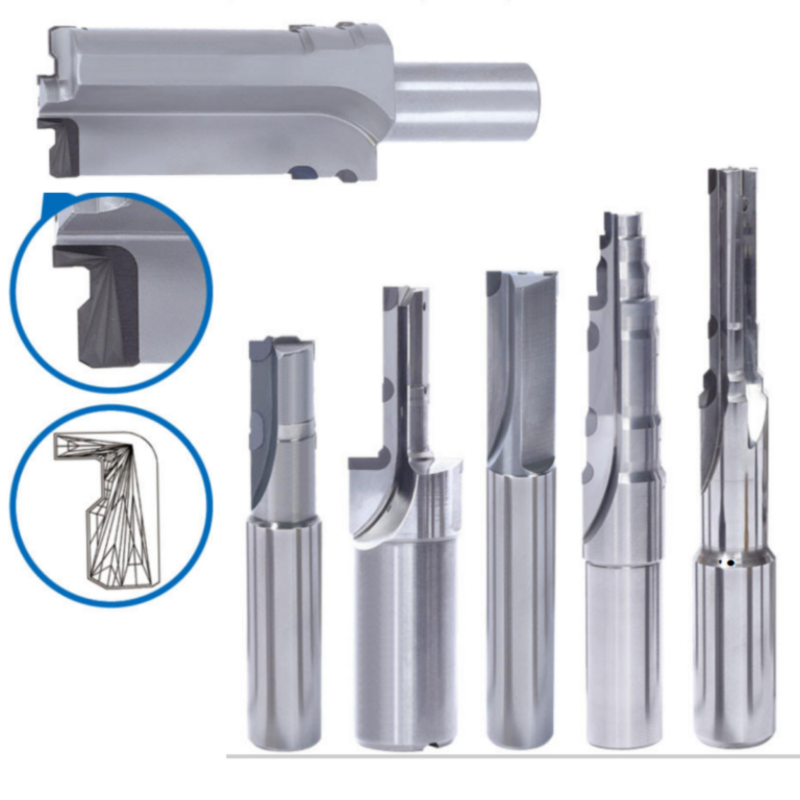
It is widely acknowledged in the industry of manufacturing that PCD tools
provide outstanding results when reaming nonferrous metals and plastics with
abrasive properties. Reaming with a PCD tool allows the user to create holes
more quickly, to tighter tolerances and produce cleaner-edge holes that are not
possible using carbide or HSS tools.
Furthermore, pcd reamer
manufacturer can produce sharper edges and decrease or eliminate the need
for secondary finishing processes such as deburring. This can help reduce the
overall cost of production.
PCD Reamers can provide consistent results for longer than conventional
counterparts because the process is not constantly interrupted to change
equipment.
For a manufacturer engaged in steady production, a carbide device might last
a few days to a week, while a PCD tool can last for months.
The experience of production reaming, the extended tool life pcd reamer
combination can provide an advantage, as well as a reduction in secondary
operations, typically results in a cost per hole that equals 20 percent of the
hole's cost when the reamer is made of carbide.
In addition to high-volume-production facilities, job shops can achieve
savings with PCD reamers. This is because the useful life of the tool is
dependent on the total number of holes that have been reamed. It does not matter
the number of projects involved.
The PCD reamers' speed is considerably faster than those made from carbide.
Carbide reamers usually operate at about 2,500 per minute. PCD reamers must be
running at 8,000-12,000 RPM to operate efficiently. PCD can produce inferior
results when it is operated at the same speed that carbide reamers do.
For large-diameter holes However, a PCD reamer can still perform at speeds as
low as 6,000 rpm.
Although the requirement for PCD reamers that run at higher speeds could make
them unsuitable for some older machine tools, most machines in use today can run
at higher speeds. The increased speed can increase productivity and lead to
faster delivery of the finished product to customers. In some cases the improved
productivity is enough to justify the investment in a faster machine.
PCD reamers have their limitations. They are not able to work with ferrous
materials, for example. They can however be reaming aluminum, brass copper,
carbide bronze and abrasive materials, such as certain of the plastics that are
advanced utilized in automotive and aerospace manufacturing.
Furthermore, PCD reamers are often three times more expensive than comparable
carbide products. The cost is enough to deter some firms from looking into the
possibility of using this technology.
Another factor that has limited businesses from implementing pcd reamer
combination in the past has been their lengthy delivery times, which can be 14
weeks or more. This was partly due lower demand for these tools, but this did
not drive toolmakers to focus on efficient ways of producing these
tools.
Today, however, thanks to growing demand and advanced manufacturing
techniques developed by the makers of PCD tools, the time to deliver have been
dramatically cut down. A standard PCD reamer could be delivered within 48 hours
and specials within 3-4 weeks.
Wider Market Opportunities
Market opportunities have opened up for PCD Reamers because of recent changes
in manufacturing. Particularly, the rising utilization of aluminum in the
manufacture of components for aerospace and automotive engines components, and
the use of metal-matrix composites to lower the weight of vehicles has boosted
the demand for PCD reamers. These materials can only be successfully machined
with PCD tooling.
Aluminum engine blocks also require the larger holes that PCD reaming makes
to attain the required performance levels. The same can be said about the
increased use of abrasive plastics within aerospace and automotive
manufacturing.
Plastics-based products and innovative, advanced workpiece materials are
rapidly replacing metals. This group of extremely challenging-to-machine
materials can limit a carbide reamer's effective life to approximately 100
holes, while a PCD tool can ream more than 3,000 holes before needing to be
replaced.
There will be more applications for PCD reamers as changes in the market occur. Parts producers will be able get contracts since they are able to efficiently machine new materials.
No comments:
Post a Comment